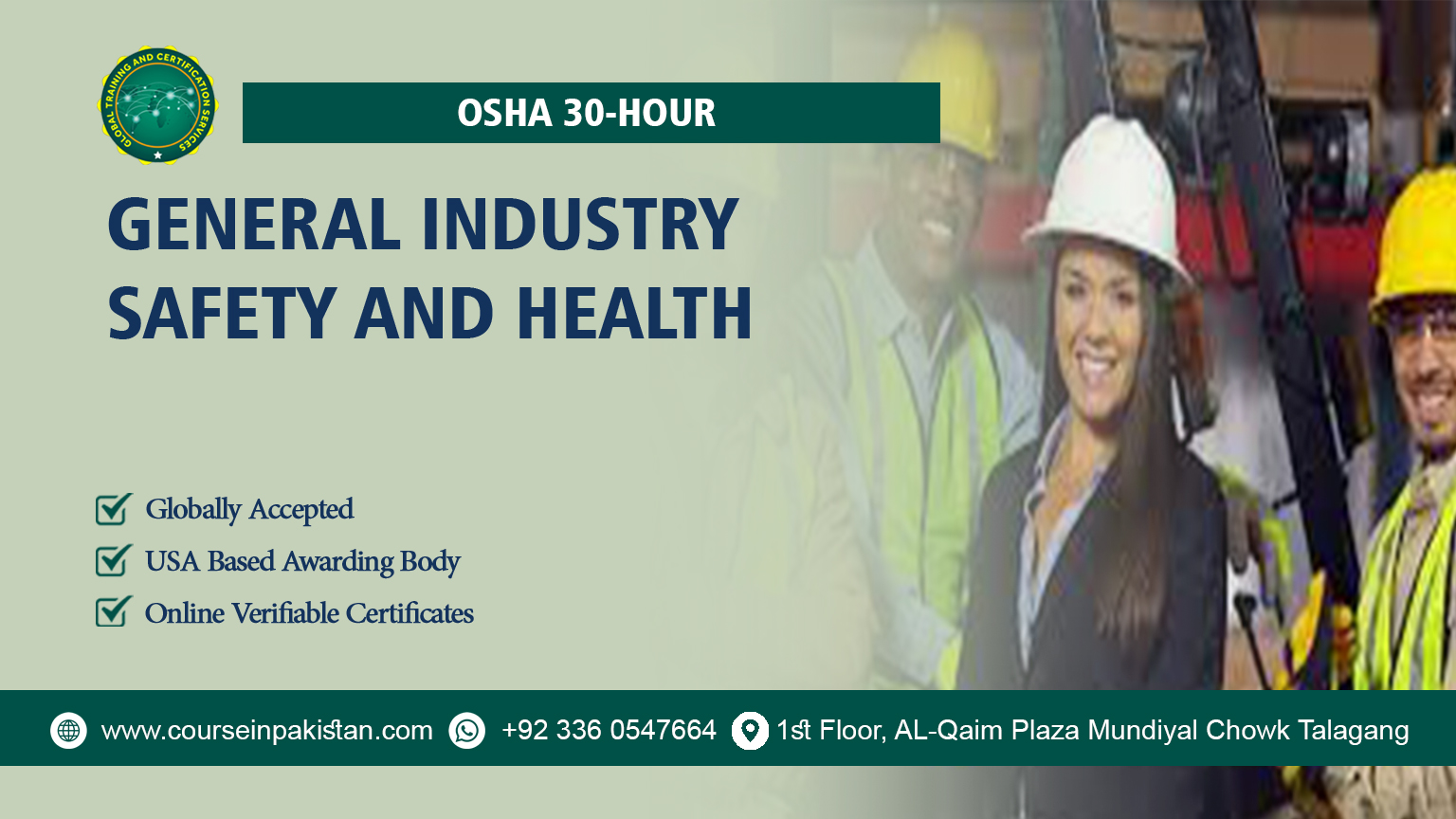
OSHA 30-Hour General Industry Safety and Health
In today’s complex work environments, safeguarding employees and ensuring a safe workplace are paramount. The OSHA 30-Hour General Industry Safety and Health course is a robust program designed to equip workers and safety professionals with the essential knowledge and skills needed to promote a culture of safety in various industries. Whether you’re new to the field or seeking to deepen your understanding, this course provides a comprehensive foundation in general industry safety standards. Here’s an in-depth look at what makes the OSHA 30-Hour course a crucial investment for your career and workplace safety.
The OSHA 30-Hour General Industry Safety and Health course is a widely recognized program offered by the Occupational Safety and Health Administration (OSHA) and accredited institutions. This course is designed to provide a thorough overview of safety and health regulations and practices specific to general industry settings. Over the span of 30 hours, participants will gain critical insights into OSHA standards, hazard identification, and effective safety management techniques.
The OSHA 30-Hour course is structured to deliver a comprehensive understanding of safety principles and regulatory requirements. It combines lectures, interactive discussions, and practical exercises to ensure participants not only learn but also apply safety concepts effectively. The course covers a broad spectrum of topics relevant to general industry, focusing on best practices for creating and maintaining a safe work environment.
Course Benefits
- In-Depth Understanding: Gain a detailed understanding of OSHA regulations and safety standards applicable to general industry.
- Enhanced Safety Skills: Learn to identify and address workplace hazards, implement safety measures, and foster a safety culture.
- Certification: Receive a valuable OSHA 30-Hour General Industry Safety and Health card, which enhances your credentials and demonstrates your commitment to safety.
- Career Advancement: Improve your qualifications for safety-related positions and increase your professional marketability.
- Compliance Assurance: Help your organization comply with OSHA regulations and reduce the risk of workplace accidents and penalties.
Course Study Units
The OSHA 30-Hour General Industry Safety and Health course is divided into several key study units, each focusing on essential aspects of workplace safety:
- Introduction to OSHA
- Hazard Recognition and Risk Assessment
- Health Hazards in General Industry
- Emergency Preparedness and Response
- Safety Management Systems
- Electrical Safety
- Machine Guarding and Safety
- Fall Protection
- Material Handling and Ergonomics
- Hazard Communication
- Confined Space Entry
- Industrial Hygiene and Environmental Health
- Fire Protection and Prevention
- Workplace Violence and Security
- Legal and Ethical Consideration
Learning Outcomes
Upon successful completion of the OSHA 30-Hour General Industry Safety and Health course, participants will be able to:
- 1. Introduction to OSHA
- OSHA Overview: Understand the role, mission, and structure of the Occupational Safety and Health Administration (OSHA) in promoting workplace safety.
- Regulatory Framework: Identify key OSHA regulations and standards that apply to general industry settings.
- Rights and Responsibilities: Explain the rights and responsibilities of employers and employees under OSHA regulations.
2. Hazard Recognition and Risk Assessment
- Hazard Identification: Identify various types of workplace hazards, including physical, chemical, biological, and ergonomic risks.
- Risk Assessment Techniques: Apply risk assessment techniques to evaluate the potential severity and likelihood of identified hazards.
- Control Measures: Develop and implement appropriate control measures to mitigate identified risks.
3. Health Hazards in General Industry
- Health Hazard Identification: Recognize common health hazards in general industry, such as chemical exposure, noise, and biological agents.
- Prevention Strategies: Implement strategies and controls to prevent or minimize health risks in the workplace.
- Health Surveillance: Establish health surveillance programs to monitor and manage exposure-related health issues.
4. Emergency Preparedness and Response
- Emergency Plans: Develop and implement emergency preparedness plans tailored to various potential emergencies.
- Response Procedures: Execute appropriate response procedures during emergencies, including evacuation and first aid.
- Coordination and Drills: Coordinate with emergency response teams and conduct regular emergency drills to ensure preparedness.
5. Safety Management Systems
- System Development: Design and implement safety management systems that integrate safety practices into organizational processes.
- Program Evaluation: Evaluate the effectiveness of safety programs and make necessary adjustments to improve safety performance.
- Continuous Improvement: Promote continuous improvement in safety management through regular reviews and updates.
6. Electrical Safety
- Electrical Hazards: Identify and address common electrical hazards in the workplace, including shock, arc flash, and fire risks.
- Safety Standards: Apply electrical safety standards and best practices to prevent electrical accidents and injuries.
- Inspection and Maintenance: Perform regular inspections and maintenance on electrical systems and equipment.
7. Machine Guarding and Safety
- Machine Guarding Requirements: Implement machine guarding requirements to protect workers from machine-related injuries.
- Safety Devices: Utilize safety devices and interlocks to enhance machine safety.
- Training: Educate employees on safe machine operation and the importance of proper machine guarding.
8. Fall Protection
- Fall Hazards: Identify common fall hazards in general industry settings, such as working at heights and unprotected edges.
- Fall Protection Systems: Select and implement appropriate fall protection systems, including guardrails, harnesses, and safety nets.
- Compliance: Ensure compliance with OSHA fall protection standards and best practices.
9. Material Handling and Ergonomics
- Safe Handling Techniques: Apply safe material handling techniques to prevent injuries and improve efficiency.
- Ergonomic Principles: Use ergonomic principles to design workstations and tasks that reduce strain and prevent musculoskeletal disorders.
- Training and Implementation: Develop and deliver training programs on safe material handling and ergonomic practices.
10. Hazard Communication
- Hazard Communication Standards: Understand and apply OSHA’s Hazard Communication Standard (HCS), including labeling and safety data sheets (SDS).
- Effective Communication: Develop effective hazard communication programs to ensure employees are aware of chemical hazards and safe handling procedures.
- Training Requirements: Implement training programs to educate employees on hazard communication requirements and practices.
11. Confined Space Entry
- Confined Space Hazards: Identify hazards associated with confined spaces, such as atmospheric hazards and limited access.
- Entry Procedures: Develop and follow procedures for safe confined space entry, including permits and monitoring.
- Emergency Response: Implement emergency response plans for confined space incidents and ensure proper rescue procedures are in place.
12. Industrial Hygiene and Environmental Health
- Industrial Hygiene Practices: Apply industrial hygiene practices to assess and control workplace health risks related to chemical, biological, and physical agents.
- Environmental Health: Implement environmental health practices to manage workplace conditions that affect employee health.
- Monitoring and Control: Use monitoring and control measures to ensure a safe and healthy work environment.
13. Fire Protection and Prevention
- Fire Hazards: Identify common fire hazards in the workplace and assess fire risks.
- Fire Prevention Strategies: Implement fire prevention strategies, including proper storage of flammable materials and maintenance of fire protection systems.
- Emergency Procedures: Develop and execute fire emergency procedures, including evacuation plans and fire drills.
14. Workplace Violence and Security
- Violence Prevention: Identify potential sources of workplace violence and implement strategies to prevent violent incidents.
- Security Measures: Develop and apply security measures to protect employees and property from theft and violence.
- Training and Response: Train employees on recognizing and responding to workplace violence and security threats.
15. Legal and Ethical Considerations
- Legal Responsibilities: Understand the legal responsibilities of employers and employees under OSHA regulations and other relevant laws.
- Ethical Practices: Promote ethical practices in safety management, including transparency and fairness in implementing safety policies.
- Compliance and Reporting: Ensure compliance with legal requirements and develop procedures for reporting safety concerns and violations.
Each unit of the OSHA 30-Hour General Industry Safety and Health course is designed to equip participants with the knowledge and skills necessary to address a wide range of safety and health issues in general industry settings. By mastering these learning outcomes, individuals will be well-prepared to enhance workplace safety, ensure regulatory compliance, and contribute to a positive safety culture within their organizations.
Who is This Course For?
The OSHA 30-Hour General Industry Safety and Health course is ideal for:
- Safety Professionals: Individuals responsible for managing safety programs and ensuring compliance with OSHA regulations.
- Managers and Supervisors: Those who oversee operations and are involved in maintaining a safe work environment.
- Health and Safety Committees: Members of safety committees looking to enhance their knowledge and skills in workplace safety.
- New Entrants: Individuals seeking to start a career in occupational safety and health with a strong foundational knowledge.
Future Progression
After completing the OSHA 30-Hour General Industry Safety and Health course, participants have several pathways for further development:
- Advanced Certifications: Pursue advanced certifications such as the Certified Safety Professional (CSP) or Certified Industrial Hygienist (CIH) to specialize further.
- Specialized Training: Engage in specialized training in areas like environmental safety, construction safety, or industrial hygiene.
- Leadership Roles: Move into leadership or managerial positions in safety and health, leveraging your enhanced skills and knowledge.
- Continued Education: Stay updated with the latest safety trends and regulations through continued education and professional development opportunities.
the OSHA 30-Hour General Industry Safety and Health course is a vital resource for anyone looking to deepen their understanding of workplace safety and enhance their professional qualifications. By investing time in this course, you not only advance your career but also contribute to creating safer and more compliant workplaces. Embrace the opportunity to become a safety champion and make a lasting impact on your organization’s safety culture.